TECHNOLOGY
Robots Help Prevent Leaks and Improve Inspection for Pipe Networks
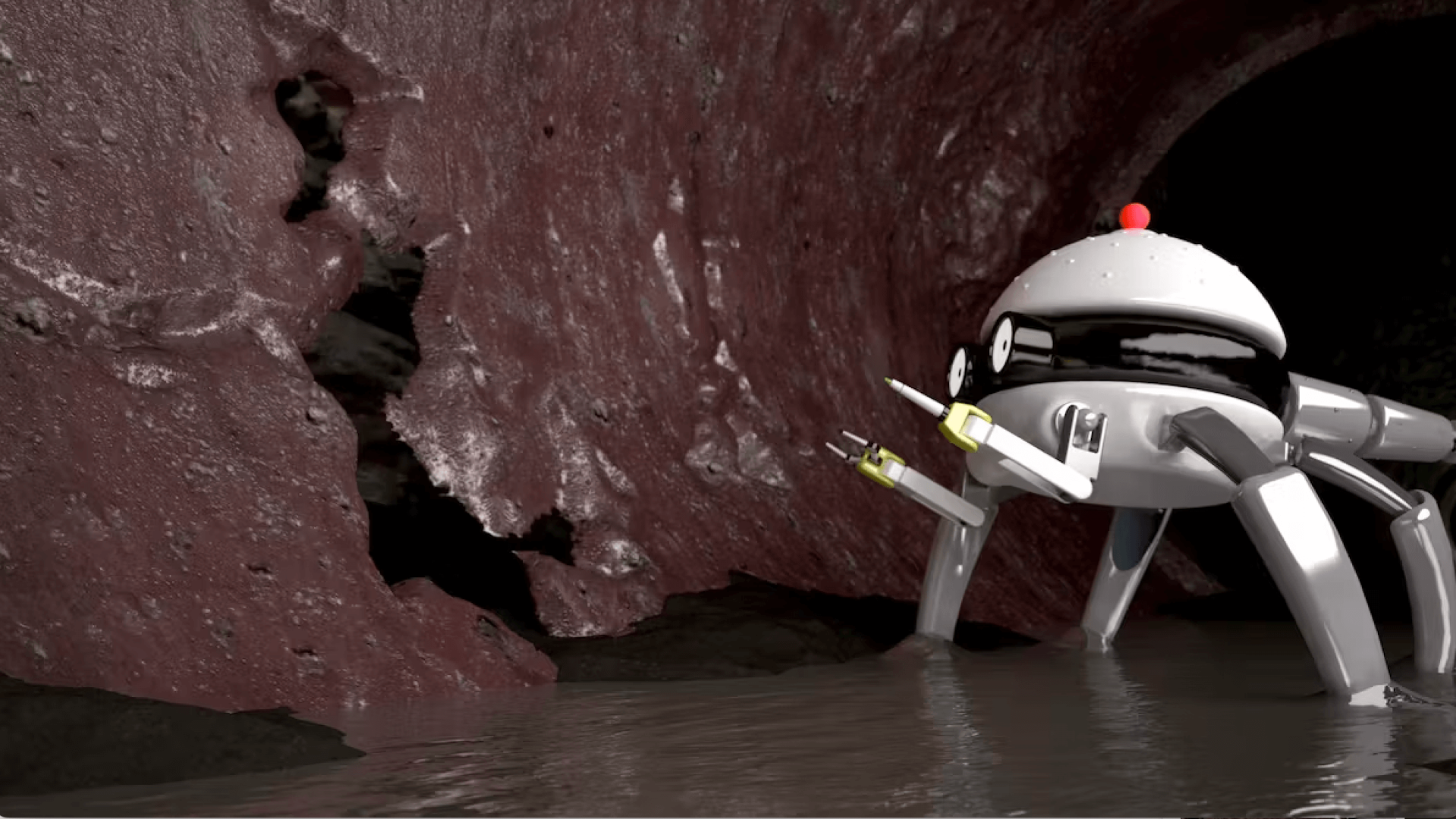
Underground utilities might be out of sight, but they are vital to our everyday lives.
Robotic pipe inspection helps utility providers maintain the underground infrastructure transporting water to millions. How do robots inspect pipes, prevent leaks and improve utility maintenance?
How Robotic Pipe Inspection Works
Robotic pipe inspection is becoming increasingly popular thanks to recent advances in engineering. It’s possible today to build small, nimble, waterproof robots perfect for navigating the unique environment of underground pipes. There are many distinct pipe inspection robots on the market, but most take a similar approach to the task.
Utility inspectors start by bringing the robot to an entry point for the pipe system they want to investigate, such as a maintenance hole. Most pipe inspection robots are tethered and remote-controlled so the inspector can see a live feed from the robot’s camera and direct where it goes. Wheels are the most common form of movement, but some pipe inspection robots also use worm-like designs that help them fit into narrower pipes.
The tether might sound unwieldy, but it serves a few essential functions. This extra-long cable powers the robot, so it doesn’t need a battery pack and can’t die in a pipe. It also transmits data from the robot to an inspector’s aboveground computer. Additionally, the tether allows inspectors to retrieve the robot if something goes wrong.
Cameras and sensors on the robot allow it to collect information about underground utilities, including leak detection. Some robots act mainly as remote-controlled cameras. In this case, the inspector will use the cameras to scan the pipes visually for signs of a leak. If one is spotted, the robot records the location for repairs.
Other pipe inspection robots use sensors to paint a picture of what’s happening inside a pipe. Sensors are crucial for autonomous robotic pipe inspection, where a human is not watching robot footage in real-time. In this case, sensor data and camera footage are used to identify signs of leaks, such as excess moisture, visual pipe damage or debris buildup. Some waterproof robots can even detect water pollution in addition to finding leaky pipes.
Innovating the Underground Utilities Industry
Why use robotic pipe inspection rather than traditional inspection methods? This technology has some amazing benefits, including an easier, safer inspection process.
Less Destructive Inspections and Repairs
One of the most significant benefits of robotic pipe inspection is its non-destructive nature. Inspecting pipes often required digging them up in the past since inspectors had no other way of seeing buried utility infrastructure. Digging is time and resource intensive. It also creates noise and physically disrupts the surrounding environment.
In contrast, robotic pipe inspection is quiet, fast and requires no digging. This reduces the cost of inspections and prevents possible unnecessary damage to pipes. During installation, pipes need layers of insulation to prevent leaks, cracks and damage and provide a vapour barrier. Digging up pipes to inspect them could damage these carefully installed insulation systems.
If inspection robots spot signs of a leak, a repair group can dig up a specific section of pipes without disrupting other areas. This system minimises the digging necessary by concentrating only on sections of pipe confirmed to have leaks or further damage.
Improved Safety
Automating underground utilities inspection improves job safety for utility workers. Annual injury rates are falling in the utility industry due to a combination of factors such as improved safety practises and the integration of new technologies. Robots can make underground pipe inspection safer by reducing the physical work required.
While many pipe systems are too narrow for humans to enter, the physical work required to dig up and manually inspect pipes can lead to injuries. For example, a utility inspector could cut their hand while working with digging equipment. The trenches required for working with buried structures like pipes also increase the risk of injury.
With robots, fewer utility workers are necessary for inspections, instantly reducing the risk of injury. Additionally, very little equipment is required and what is needed is generally harmless. Most robots are controlled with a laptop or tablet, which is in more danger of damage than a utility worker. The robot also goes underground instead of a person, eliminating risks like pipe or trench collapse.
Simplified Inspection Process
The underground utilities inspection process is much faster and easier than conventional inspection methods. Robotic pipe inspection allows one or two people to inspect a whole network of pipes with just a computer and the robot’s required gear. They don’t have to dig or survey the land, so the process of conducting an inspection is simple and straightforward.
Easy underground utilities inspection is important for improving the quality of pipe maintenance. Inspections are performed less frequently when they are expensive and time consuming to conduct. Quick, easy, low-cost inspections allow utility providers to perform more frequent inspections which allows them to catch cracks, leaks and other potential problems sooner.
Early leak detection minimises the negative impact of leaks and results in smaller repairs. It also reduces the risk of a small leak worsening into a much bigger issue. For example, pipe leaks can allow contaminants into pipe networks, creating health and structural risks. Catching leaks early prevents serious side effects from taking root.
The Future of Underground Utilities Robots
Robotic utilities inspection is a relatively new technology that became widely accessible in the last few years. As adoption grows, developers and researchers are hard at work creating more advanced robots. How will the technology change and improve down the road?
Modern underground utilities inspection robots usually require a tether and remote control. In the future, they could be fully autonomous and fully wireless. Some robots may retain a tether for use in a mechanical failure or malfunction.
Fully autonomous pipe inspection robots will allow utility providers to have 24/7 pipe monitoring. Early versions of these robots use AI to operate and communicate with the robots and collect data through cameras and sensors. For example, researchers at the University of Sheffield developed fully autonomous pipe crawler robots that use microphones to listen to the pipes and analyse the sounds for signs of leaks.
Along with fully autonomous inspections, underground utilities robots may one day be able to conduct minor repairs. For example, if an autonomous inspection robot spots an emerging crack, it can patch it before it creates a leak. This technology isn’t available yet, but one day it could be a reality, likely by integrating 3D printing technology into pipe crawler robots.
The Incredible World of Robotic Pipe Inspection
Robotic pipe inspection is a groundbreaking milestone in underground utilities maintenance, although it removes the need for inspectors to break the ground at all! Robots are helping utility providers take better care of pipes and perform maintenance safer, faster and for less money. In the future, pipe crawler robots could become fully autonomous, roaming pipes 24/7 with the help of AI.