OTHER
Quality Control in Electronics Manufacturing: Best Practices and Strategies
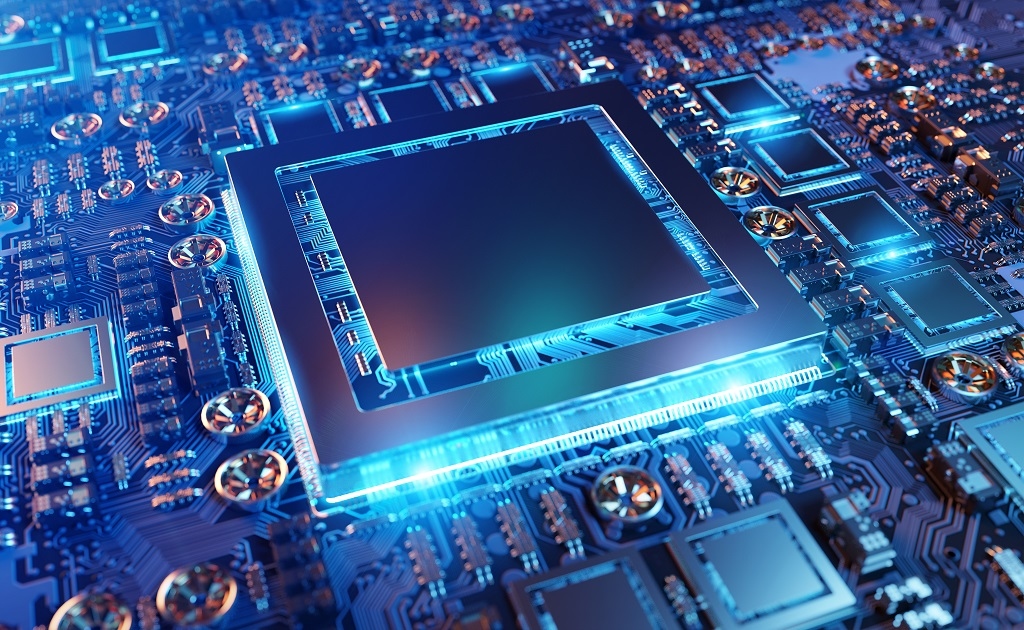
Electronic devices have become an important component of every organization and industry.
Electronic manufacturing companies can make electronic devices with different methods but maintaining the quality of the device is another thing.
He should have to make sure that he uses the best methods to maintain the quality of the final product. However, to check the quality of the device there is a system called QMS (quality management system) which is based on international standards i.e. ISO 9001, ISO 13485, and TS16949. It gives the manufacturer all the instructions to control the quality during the process of electronics manufacturing or after the final product is made.
It has different features that can be used to detect errors in electronic manufacturing services or to check defaults in the final electronic device. The QMS system also has the quality policy which gives all the important information about quality control. Moreover, it also has the instructions to guide the manufacturers during the whole electronic manufacturing services.
In this article, you will find all the necessary information that could be helpful in maintaining the quality of any electronic device. It will provide you with different strategies and steps to ensure the quality of the final electronic device. The following are the different practices and strategies that you can consider for the better quality of electronic devices.
Hiring Quality Control Experts
If you want to make sure that you produce high-quality electronic devices, you should hire a person who is great at his job. This will reduce the cost of removing the errors and the time will also be saved. Because engineers play a vital role in electronics manufacturing or other electronic manufacturing services, if you hire someone who doesn’t know what he is doing then he will cause many troubles during the electronic manufacturing services and you will not be able to provide better quality to your potential customers. Before hiring someone you can check their expertise on different companies where they are doing the PCB quality control or other electronic devices. Hiring professionals is the first important step to ensure the quality of the PCBs.
Automated Optical Inspection
Besides visual inspection, the electronics manufacturing companies can turn to visual inspection which can be done by the automated optical inspection machine. It equips a machine scanner that uses light imaging. An AOI machine typically contains many light sources and multiple cameras, sometimes including video cameras. The cameras on it can make 2D or 3D images of the devices which are of high-resolution. Therefore, it is a more reliable process than manual inspection. Because there are fewer chances of human errors as the entire process is automated. It can detect any errors in the soldering of PCB assembly. Therefore, to ensure the quality of PCB boards you should subject it to the automated optical inspection. It is also being used to test the PCBs that are produced in high volume to save time and cost.
X-Ray Inspection
Automated X-ray inspection is another strategy to check defects in PCB assembly and to make sure the quality of the PCB is not compromised. X-rays are used to examine internal features and subsurface conditions in test objects. X-ray inspection can find hidden features within a target object. It can make 2D or 3D images of the soldering paste on the PCB board. With the help of this, engineers can look for any unwanted space in the solder paste. The spectrum of use is broad and ranges from quality controls for electronics manufacturing, to the testing of materials for cracks and air inclusions, to foreign matter inclusions and shape deviations. This technique is mostly used to detect errors in small volume or prototypes. It can help you to reduce the cost of repairing the devices and it is the efficient technique that helps in maintaining the quality of the PCB board.
Functional Test
To make sure the electronic devices will work as the intention of the designer, it is better to do a functional test. It will simulate the usage situation and test if all the parameters are the same as the design. We usually need to produce functional testing fixtures first. But we should understand that it is difficult to test all the functions, but only test the main functions.
Visual Inspection
To find any errors in the PCB assembly, a visual inspection is done. The engineer may use a magnifier or he may try to find the fault in the soldering with his naked eyes. However, visual inspection is highly dependent on the skill of the worker. If he is an expert he may be able to find any errors in the assembly process. On the other hand, if the engineer is not an expert you will not be able to produce high-quality electronic devices. However, visual inspection turns out to be very effective, because it is not costly and can be done easily in electronics manufacturing.
Burn-In Testing
Burn-in testing is another technique to ensure quality control in PCB manufacturing. It is a type of stress test that involves applying extreme conditions to components or boards to eliminate failures. It can check the performance of the device in different environmental conditions. PCB boards are subjected to different temperatures, and currents to make sure that it will not burn out and will work properly once it is ready to sell. It can also be used to check the failures that may trigger in the future as well. Hence, it plays an important factor in ensuring the quality of electronic components and parts. Burn-in testing comprises two different types of tests:
-
Static Testing
-
Dynamic Testing
To Sum Up
To make sure that you are providing your customers with the best quality, an electronic manufacturing company should follow the best practices and strategies that would help you to make high-quality products and reduce the errors in electronics manufacturing. An electronic manufacturing company should have the best quality control department in your organization because it will help you to reduce human errors and poor-quality products.